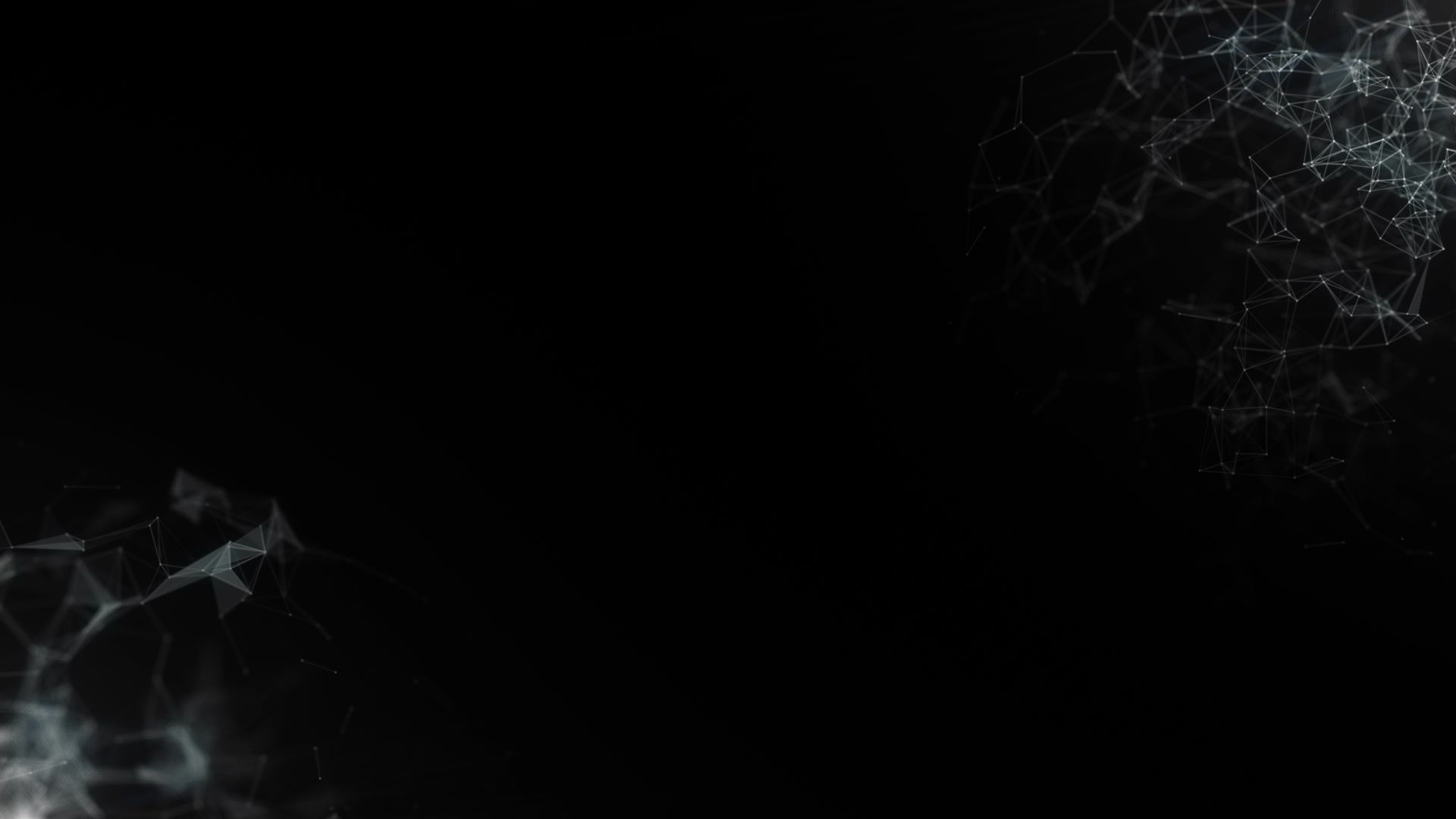
OVERVOLTAGE PROTECTION
An overvoltage protection (OVP) circuit is aimed at protecting a load (or, in general, a following circuit section) from abnormal and potentially crushing spikes of voltage supply. The proposed OVP architecture for DC power supplies is shown in Fig.1.
The circuit operation relies mainly on the Zener diode D1, since its breakdown voltage determines the threshold value of the overall circuit. In fact, until VIN remains below D1 breakdown voltage, D1 stays off in reverse polarization and no current outgoing from Q2 BJT base can flow, keeping the latter off in turn (VEB = 0). Therefore, since BJT Q1 is clearly on and in saturation (since Vbc < 0) with base current flowing through R3, in this case VIN equals VOUT (except for the VEC drop). When VIN exceeds the breakdown threshold, instead, D1 starts conducting towards ground triggering the switching on of Q2. This creates a low-resistance path between nodes IN and X, causing Q1 to switch off and the load voltage to be inhibited.
The correct operation of the circuit has been simulated in LTspice using a Zener diode with breakdown voltage of about 10 V (built-in BZX84C10L model by ON-Semiconductor), a resistive load of 10 kΩ and a voltage supply varying from 9 V to 11 V and then back to 9 V with ramp pattern. Fig.2 depicts the results of the simulation. As expected, as VIN (green track) rises above 10 V, D1 inverse current (blue track) grows more and more causing Q2 (yellow track) to conduct and, in turn, load voltage (red track) to drop to 0 V after reaching a maximum value of 10.4 V.

Fig.1 - Overvoltage protection (OVP) circuit schematic

Fig.2 - Simulation of OVP operation (LTspice)
Supposing D1 and RLOAD fixed, the exact voltage threshold of the circuit depends also on the values of R1, R3 and (much more slighty) of R2. In particular, by increasing R3 the OVP circuit acts at lower voltage levels (and, equivalently, more quickly in time) due to the weaker Q1 base current during nominal operation (i.e. when OVP is not triggered). Moreover, it is important to notice that keeping R3 high is useful for limiting power consumption in nominal operation, even though too high values (especially in relation to RLOAD) may cause Q1 to never switch on. Similarly, by increasing R1 the OVP circuit is triggered at lower voltage levels (and, equivalently, more quickly in time) since current flow through R2 is eased (R1 and R2 + Q2 can be seen as two resistive paths in parallel converging to D1) and, in turn, the switching on of Q2 fostered.
Of course, the use of this circuit can be extended to any voltage supply, OVP threshold and load values by simply acting on the choice of D1 and R3 mainly, as explained above.
Finally, component C1 acts as decoupling capacitor, good practise in order to assure a more constant supply voltage by smoothing abrupt transients and filtering noise from other circuit sections.
After the first step of study, simulation and validation of the circuit, this has been converted into a PCB by means of Altium Designer. In sight of this, another potentially useful section of circuit has been inserted. As shown in Fig.3, two more branches containing each a MOSFET, an LED and a resistor have been inserted in order to be able to visually assess the OVP circuit state. In fact, while VIN remains below threshold the high value of VOUT makes the M1 N-MOSFET conduct and, in turn, the green LED on, whereas a low value of VOUT due to an overvoltage causes M2 MOSFET conduct and, in turn, the red LED on.
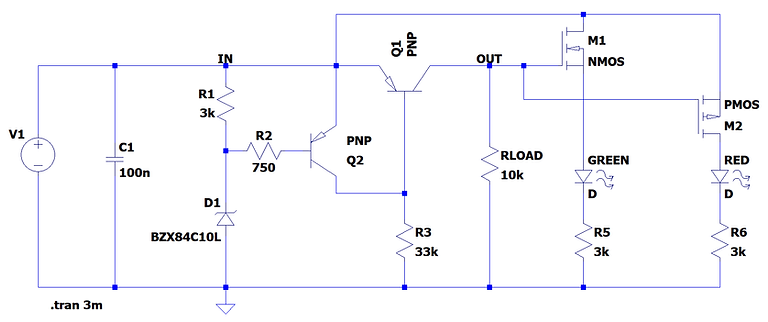
Fig.3 - Schematic with LEDs
As first step of the PCB design, components have selected from distributors websites. For the sake of simplicity, all have been chosen from Digi-Key database, paying attention they were in-stock, not outdated and provided 3D models from manufacturer. Since the voltage and power levels of this case study are contained, 0603 and 0805 packages have been picked for diodes, resistors and capacitors, common SOT23 for all transistors, and a male DB9 as I/O connector. The bill of materials (BOM) of the PCB is recapped in Fig.4 as output file from Altium.

Fig.4 - PCB BOM (Altium)
After drawing all footprints as recommended in datasheets (example for the DB9 connector is shown in Fig.5), schematic has been created and annotated, as reported in Fig.6. As next step, PCB layout has been designed following some common constraints (e.g. minimum clearance of 0.3 mm, routing width of 0.4 mm, via diameter and hole size of 0.6 and 0.3 mm respectively, etc...), rules (e.g. no right-angle routing and decoupling capacitor placement close to connector) and useful recommendations (such as placing LEDs and transistors on the top layer). The 2D and 3D layout outcome is shown respectively in Fig.7 and Fig.8. In terms of final dimensions, the board measures 42.3 x 32.8 mm with a dielectric thickness of 1.5 mm.

Fig.5 - DB9 connector 2D/3D footprint (Altium)
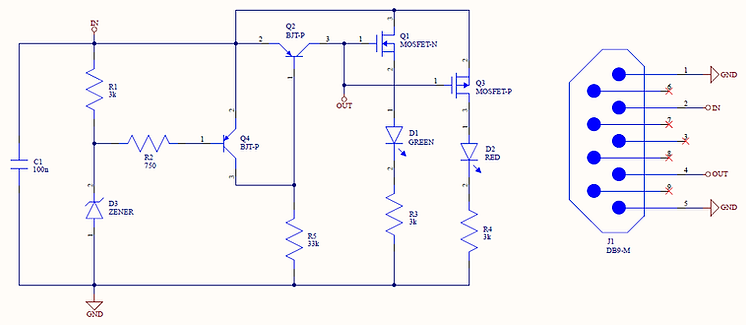
Fig.6 - PCB schematic (Altium)

Fig.7 - PCB 2D layout, top and bottom layers (Altium)
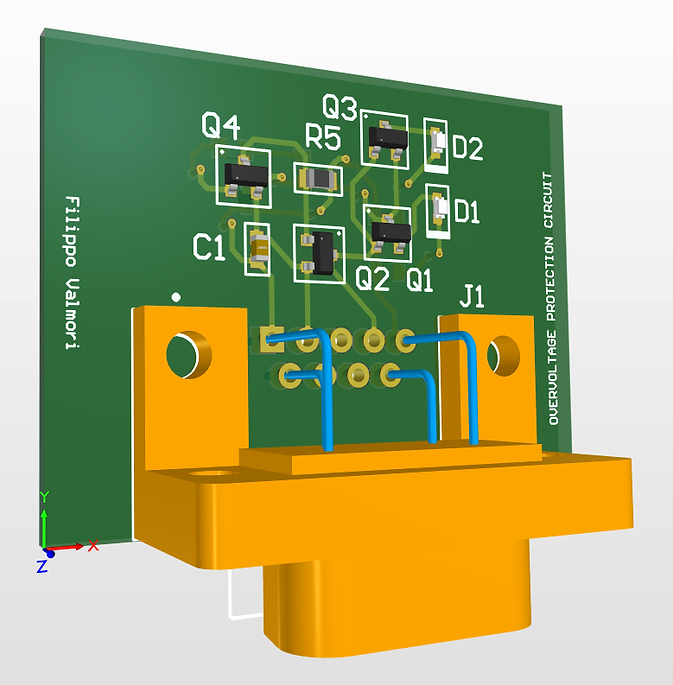
Fig.8 - PCB 3D layout (Altium)
Then, a project variant has been foreseen for the case in which the presence of the LEDs is not desired, generating the schematic of Fig.9 where all the component of the corresponding branches are set as not fitted. Finally, to complete the project all the typical manufacturing documentation has been produced, including assembly drawings (see Fig.10), Gerber, pick and place, NC drill, STEP and draftsman files. All these output files can be found in a dedicated folder inside the project shared at the bottom of the page.

Fig.9 - PCB schematic with variantion (Altium)

Fig.10 - PCB assembly drawings, top and bottom layers (Altium)
Below there are the links through which the aforementioned projects can be free downloaded. Regarding the Altium project, the main files to consider are the ones with extension .SchDoc, .PcbDoc, .SchLib and .PcbLib, containing respectively the circuit schematic, the circuit PCB, the schematic library and the PCB library (for footprints). In addition, inside folder EXTRA all datasheets and 3D models of the picked PCB components are gathered.
-
Download LTspice projects : OVP-LTspice.zip
-
Download Altium Designer projects : OVP-Altium.zip
WARNING#1: Circuit simulations and PCB design have been developed respectively in LTspice XVII and
Altium Designer 18 softwares. Therefore, their correct operation might not be assured with different softwares versions.
Last update : 22/03/2020